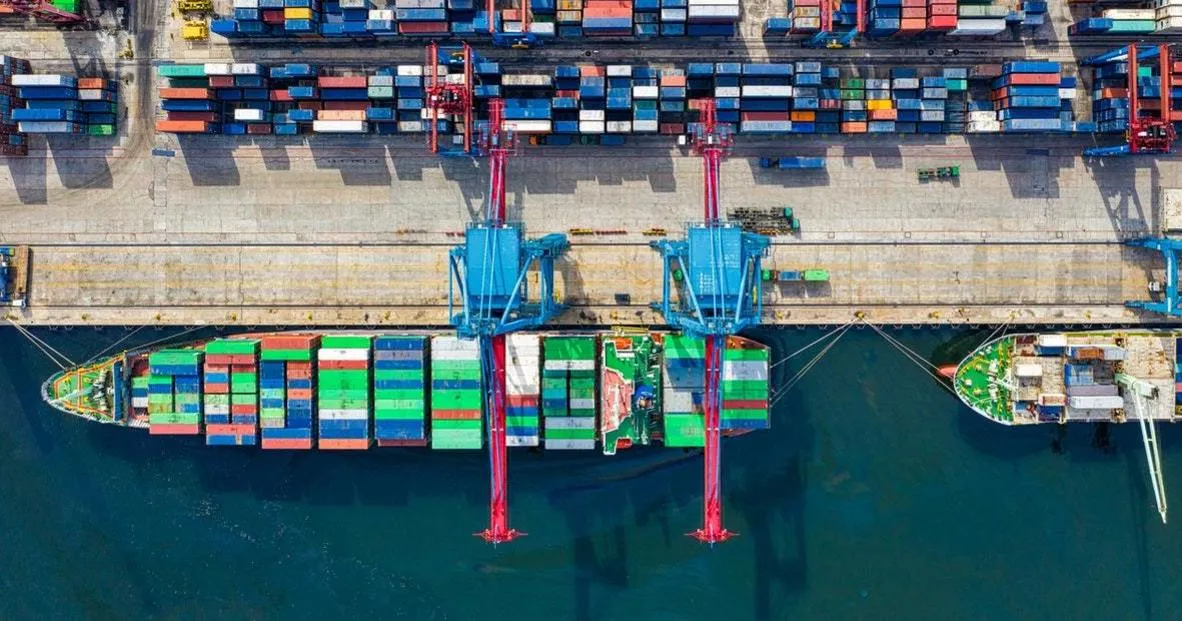
Robotic Process Automation (RPA) in Logistics And Supply Chain
18 February 2021
The Logistics and Supply Chain sector is amongst the most competitive in the world, with many companies striving for competitive advantage by lowering prices and looking for opportunities to increase efficiency.
The industry relies heavily on back-office operations that undertake the challenging job of scheduling shipments & deliveries, cross-docking, monitoring changes, handling exceptions and most importantly keeping their customers satisfied.
In order to successfully carry out these important jobs, almost all back-office employees are required to conduct manual and repetitive processes using computer systems and applications. Although these jobs are vital, they can be tedious and prone to human error resulting in a demoralized staff and unwanted problems. This is where Robotic Process Automation (RPA) can breathe new life into back-office operations.By automating rule-based tasks that are carried out on computers, RPA frees up employees and enables them to use their human judgement for tasks such as exception handling, that require more complex thinking.
RPA has been creating waves across many industry verticals and is quickly becoming a must-have tool for most digital transformation initiatives. Automation adds value by enabling organisations to work faster, increase accuracy, drive operating costs down and increase customer satisfaction.
What are The Processes That Can Be Automated In The Industry?
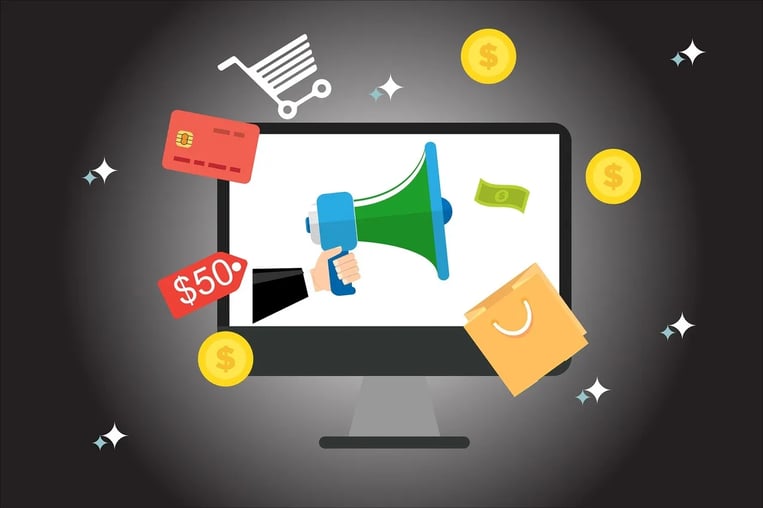
We at Cevitr have compiled a list of commonly automated processes after speaking to leading industry professionals from various Logistics & Supply Chain organisations of all sizes;
- Order Processing & Payments: Processing orders is accompanied by transactions such as manual entry of the customer's information into a database, processing the payments and sending out email confirmations for order updates.
- Onboarding of Accounts & Customers: Often there are many different portals to enter customer information, all these portals although different in the layout will have m We at Cevitr have compiled a list of commonly automated processes after speaking to leading industry professionals from various Logistics & Supply Chain organisations of all sizes;
- Order Processing & Payments: Processing orders is accompanied by transactions such as manual entry of the customer's information into a database, processing the payments and sending out email confirmations for order updates.
- 4. Onboarding of Accounts & Customers: Often there are many different portals to enter customer information, all these portals although different in the layout will have many of the same required fields and an employee is basically copying and pasting the same information numerous times.
- Shipment Scheduling and Tracking:from the initial pick-up request to checking and reporting shipment status between internal systems and portals. Extract shipment details from incoming emails, log jobs in your scheduling systems and provide pick-up times in the required portals.
- Invoicing: RPA can eliminate re-keying, cutting-and-pasting and manually attaching data to invoices, automatically extract data, attach scanned PODs and invoices and update customer portals.
- Procurement & Inventory: Ensuringinventory control is live and up-to-date is key for manufactures and suppliers to confirm that they have enough products in stock to meet demands. If the products are out of stock or below a certain threshold, the process of reordering can be done immediately through automation.
- Customer Services: Representatives deal with hundreds of queries a day. By leveraging RPA, the Customer Services Team can be assigned to focus on the more challenging queries and the software bots can be used to answer the basic non-judgement-based queries, thus delivering service levels of the highest possible standard.
Whilst RPA delivers efficiency, accuracy and reduces operational costs, a barrier to adopting this technology is the expertise required to successfully deploy RPA in-house and the cost of implementation. Many companies that are already squeezed on their margins simply do not have the capability to leverage this technology and are reluctant to make the investment.
At Cevitr, our aim is to enable businesses to leverage the power of this technology by offering Robotic Process Automation as a Service (RPAaaS) by removing the barrier of upfront investment and in-house expertise. We provide a business process outsourcing service that uses a Digital Workforce to execute business processes for and on behalf of our clients. From the initial consultation to final deployment and maintenance, we facilitate RPA enabled processes through our cloud-based platform. The RPAaaS offer is complemented by a Zero Capex savings commercial model, simplifying the deployment of RPA. We also provide the delivery of an automation roadmap that considers both the direct and consequential benefits of automation. By offering RPAaaS we are able to offer the end-to-end lifecycle of automation.
We want to enable organisations to benefit from RPA and create opportunities for them to reinvest the fantastic savings they can expect from day one.